High fives were had all around as CalSol’s Motor team recently submitted its final project proposal for the Big Ideas at Berkeley Grant Competition. But it was not long before we were back with our noses to the grindstone.
The CalSol Motor subteam (nicknamed “Rotors in Motion”) was born out of the challenges the team had getting our motor to run consistently leading up to the World Solar Challenge. While we were ultimately successful in coaxing our motor to run smoothly, the performance was still suboptimal. That, and the conviction of Professor Dennis Lieu that we could create a better machine ourselves, gave birth to our mission to design and build a new solar vehicle motor from the ground up. Specifically, we hope to introduce transverse flux technology to the solar racing community, which has hitherto relied almost entirely on a narrow selection of axial flux motors.
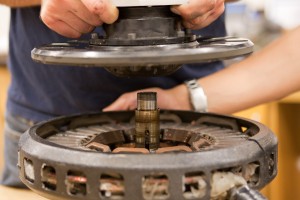
While more difficult to construct, transverse flux motors innately have about twice the energy density of axial flux motors. This means that for the same power output, a transverse flux motor can be about half the size of an axial flux motor. In addition to saving weight on the motor itself, this allows for a slimmer rear suspension and wheel fairing, which are indispensible attributes in a solar racer.
Furthermore, building our own motor allows us to design specifically to the technical restrictions placed on vehicles by the North American and World Solar Challenges. These regulations have evolved since the last generation of solar vehicle motors was designed, reducing the amount of solar energy a car can harness. This renders motors designed for higher power inputs less advantageous than they were at the time of their invention one to two decades ago (depending on manufacturer).
In order to successfully parameterize the motor, requirements such as maximum torque required and maximum achievable continuous power, amount of ventilation/cooling necessary need to be calculated. To this end, we are performing analysis on data collected during the recent World Solar Challenge as well as performing new experiments on the motor currently inside Impulse.
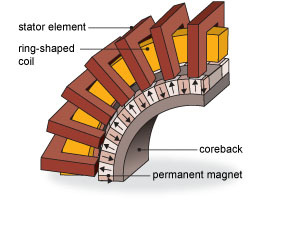
Happily we have already made significant progress towards this milestone. We have concretely determined the maximum allowable temperature of the motor and made first calculations of the necessary stall torque, the average, realistic charge per day of the solar cells will provide, drag area, and rolling resistance constants. At the moment in addition to double checking those calculations, we are working on new coast-down experiments to more accurately analyze the dynamic resistances the motor must overcome during continuous operation. Lastly, we will be load testing the motor in Impulse to evaluate the convection inside the solar car’s rear fairing.
With regards to the motor’s mechanical design, Professor Lieu has given us a special workshop in spindle design, which will be our first area of focus. Based on the parameters we determine in the aforementioned tests, we will determine a volume envelope within which the motor must be built, and then design will immediately begin on our spindle.
There is a long road ahead of us. With a system this intricate, where delicate changes have profound results, attention to detail, extremely careful analysis, and extensive testing are vital. The process will doubtlessly take a few years, but we are excited to tackle this uncharted territory.