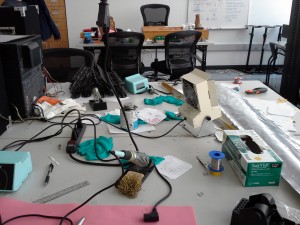
The electrical team has been making good headway lately, with new, experienced, and alumni members all working to finish the assembly, testing, and troubleshooting of Zephyr’s electrical system.
The HCI (Human Control Interface) sub-systems are able to communicate among themselves over the CAN bus, which stands for Controller Area Network and allows for communication without a central computer. These sub-systems include the dashboard, accelerator and brake, steering wheel and side panel, and the two motor controller controller (which controls the motor controller, and is dubbed the MC^2). The controllers are working, and the motors are able to spin.
Regarding the solar cells, the solar array is coming together, with the team ready to finish placing the cells. The MPPT’s (Maximum Power Point Trackers, which keep the solar array at an optimal power output by manipulating on the I-V curve) are able to communicate over CAN as well.
Additionally, the two power hubs (which distribute power to the various electrical systems, which need to be kept on lines of separate voltages) are ready, and the BMS (Battery Management System) seems to be operational. All the electrical boards have been soldered, populated with components, and tested. The battery box has been built, and the fuses, connectors, and peripherals are being mounted.
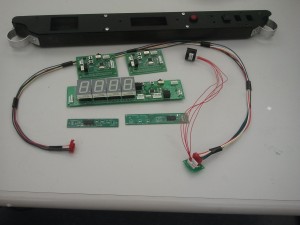
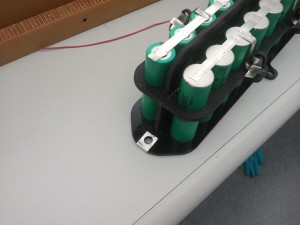

We couldn’t have done this without the financial and technical support of our sponsors:
Advanced Circuits, for producing many of Zephyr’s PCB’s!
Bay Area Circuits, also for producing many of Zephyr’s PCB’s!
LEMO, for donating connectors!
Phoenix Contact, also for donating connectors!
Linear Technology, for giving LT boards and chips, providing monetary donations, as well as technical support and guidance!
Thanks for catching up with us, and see you soon!